Successful vibration test runs
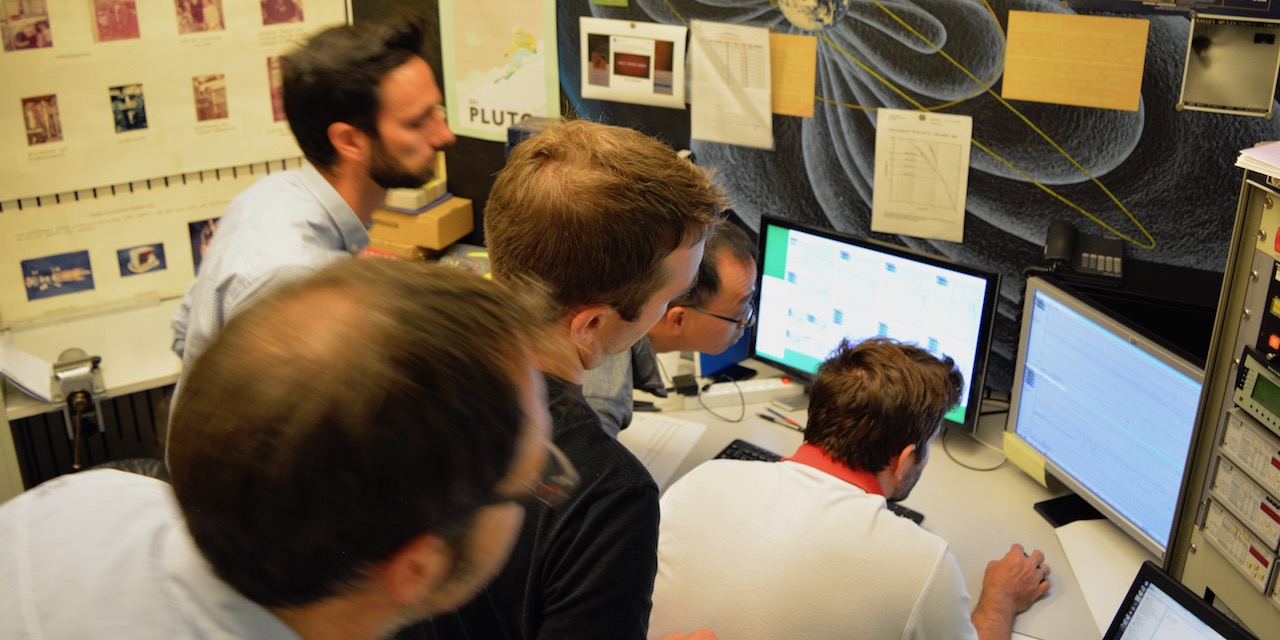
During ten days in August 2017, the CHEOPS telescope had to withstand various tests on the shaker at the University of Bern simulating the conditions during the launch with a Soyuz rocket. The experiments were successful – a big step towards the completion of the flight model.
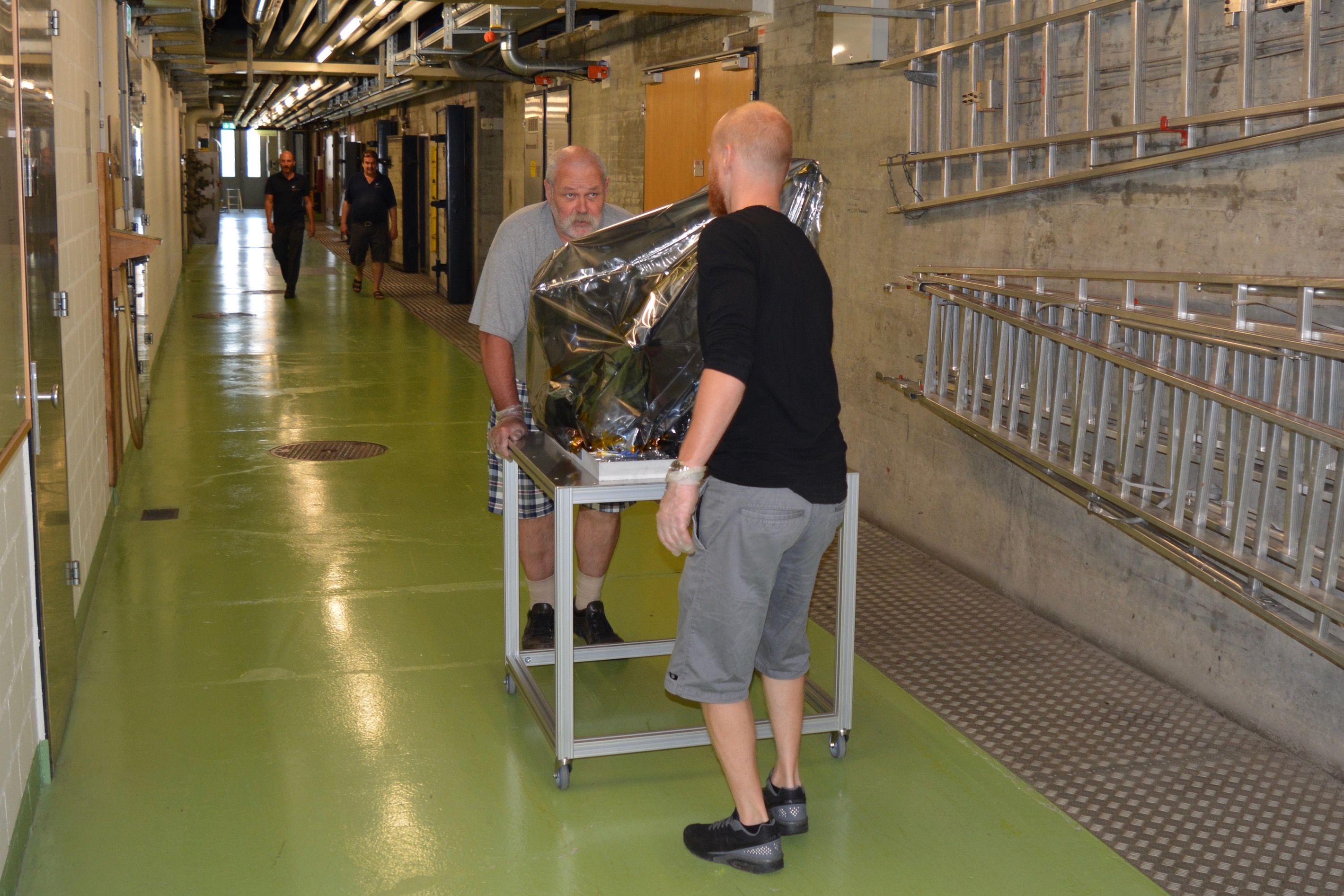
Engineers Daniel Schaedeli and Martin-Diego Busch transport the CHEOPS telescope. (Photo PlanetS)
The small control room in the shaker laboratory at the University of Bern is crowded on this sticky afternoon, on 15 August 2017. Besides the engineers who conduct the tests of the CHEOPS telescope, the team leaders as well as representatives from ESA and the Italian mirror factory are present to follow one of the last of a series of vibration tests: «Sine 100% z-Axis» is written in red letters on a paper that system engineer Thomas Beck places in front of the video camera installed to document the test run. «The z-axis is the most critical one for the telescope mirror», explains Christopher Broeg, CHEOPS project manager.
Before, the instrument had to pass several vibration runs in its x- and y-axis. To protect the telescope against pollution, the engineers had wrapped the flight model in three layers of plastic foil filled with very clean and dry Nitrogen before they transported it from the clean room to the shaker lab deep down in the cellar at the other end of the building. There, it was mounted on the shaker using a special gantry. For the tests in the x- and y-axis, the engineers screwed the instrument to a horizontal table with the vibration machine pushing from the side, whereas it is now fixed to a vertical table on top of the shaker.
The upcoming sine test is one of two test regimes carried out during the last ten days. The shaker imparts sinusoidal acceleration at increasing frequency up to 120 Hertz. The other method is called random testing: The machine provides vibration at multiple frequencies simultaneously with randomly varying acceleration. In-between each test (both random and sine), a so-called resonance search is performed: Like the sine test the instrument is shaken at increasing frequency but at a very low level from 5 Hz all the way to 2000 Hz. Accelerometers attached to many pieces of the instrument measure the instrument response. If a structure is damaged, the corresponding response would change. Therefore, after each tests the engineers check that the responses remain unchanged.
«The sine tests are performed to validate that the hardware can withstand the static forces of the launch, whereas the random tests serve to simulate the vibro-acoustic spectrum of the rocket engines», explains Thomas Beck. For both types of tests, the engineers started with low loads and increased them gradually until parts of the instruments had to withstand accelerations of more than 10 g. «We have already completed a lot of tests», says the project manager: «We are approaching the limit slowly step by step.»
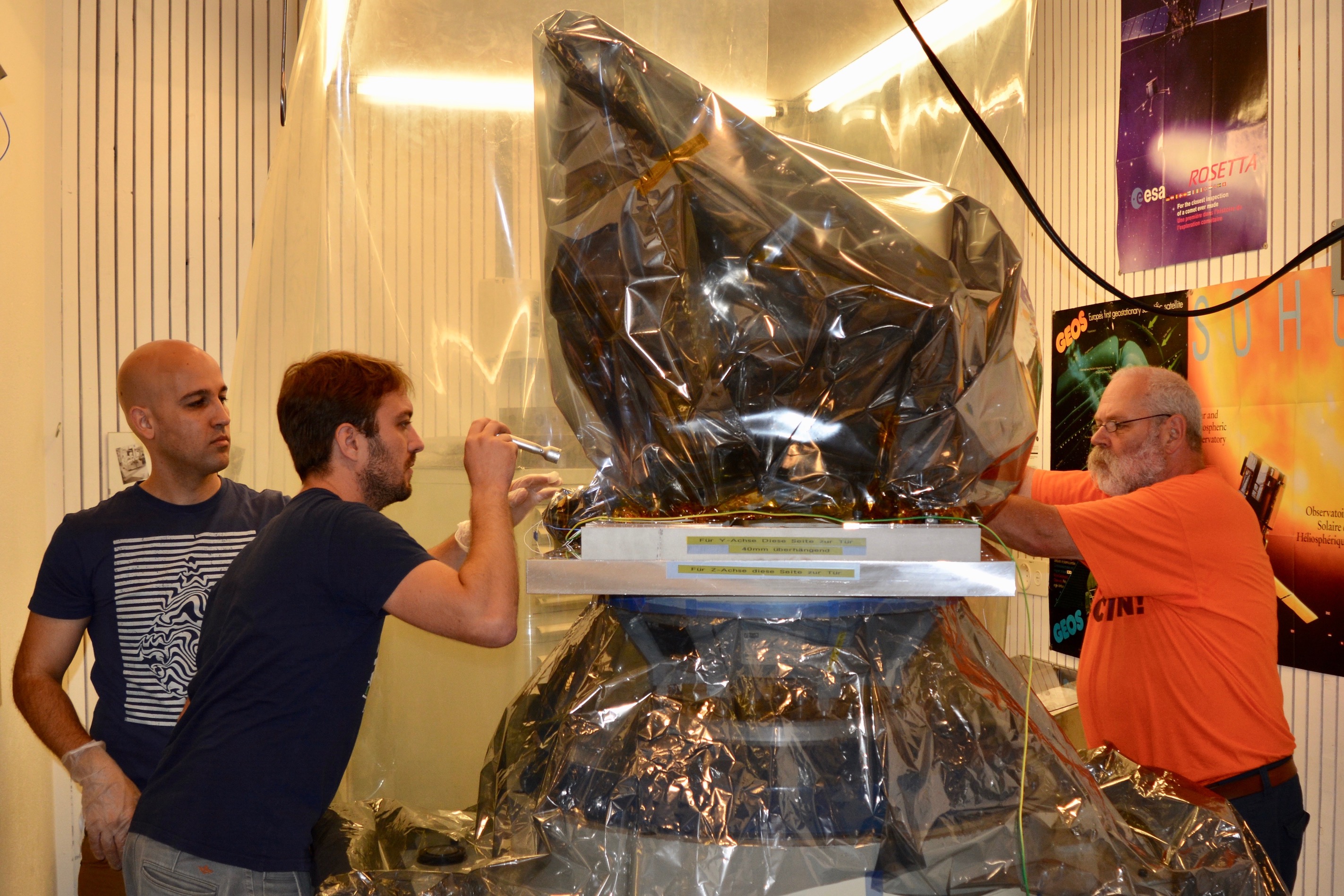
Eduardo Hernández, Thomas Beck and Daniel Schaedeli prepare the telescope for the tests.
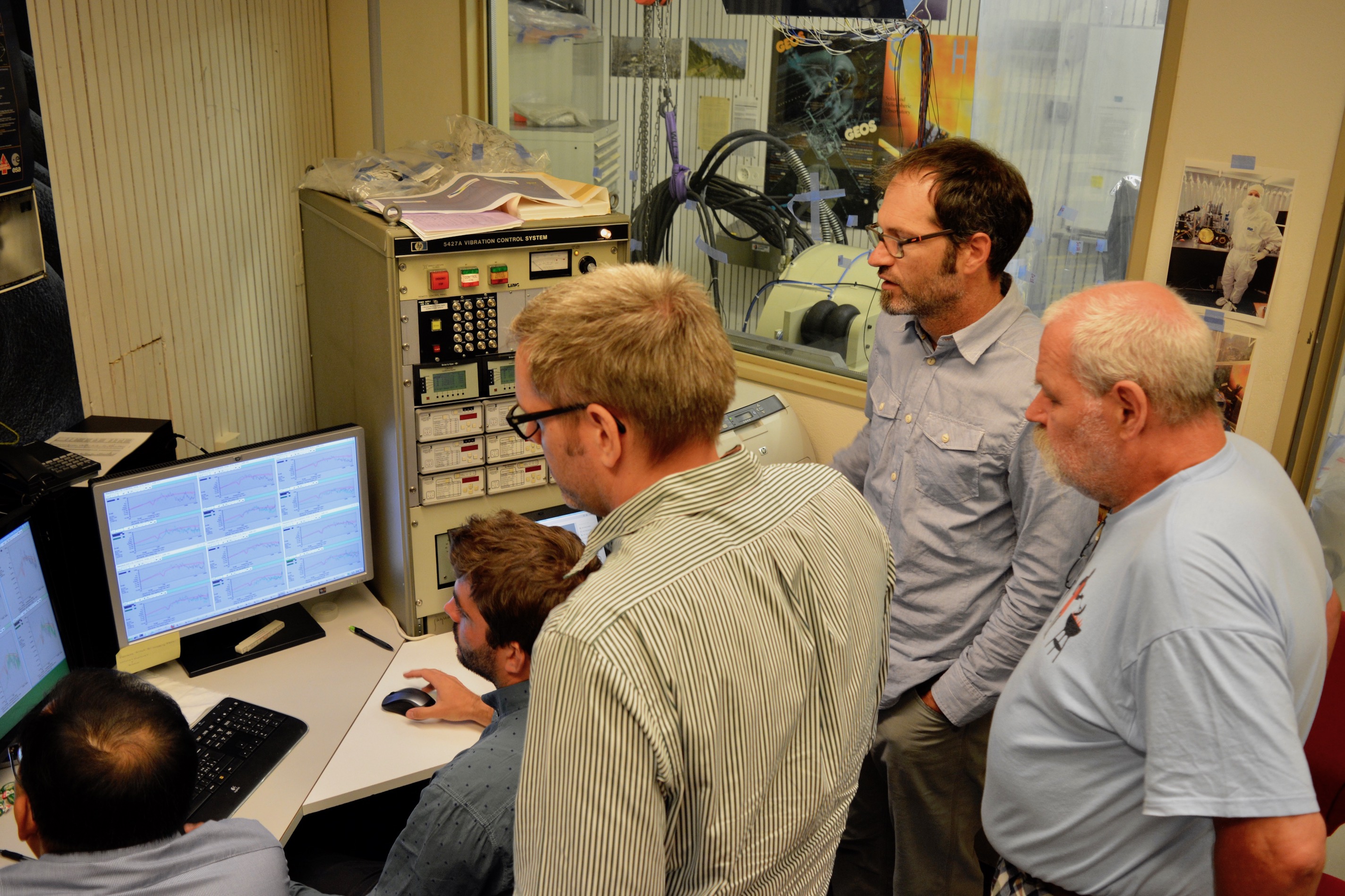
The CHEOPS team looks at the results in the control room. (Photos PlanetS)
Every test is a risk
So far, all the experiments run smoothly and the engineers are confident that also the sine test at full load in the z-axis will be successful. But they know that every test is a risk that something might break. The tension in the control room is palpable. «Is there anyone who isn’t nervous?» asks test engineer Daniel Schaedeli. «Is everything strapped down enough?» someone wants to know. Then the machine starts, the telescope begins to bounce. Within seconds the first still moderate hops get bigger and much faster, the rustling noise changes to a swelling sound as if something would take off – fortunately not.
After one minute the shaking is over. Nothing unexpected happened. But the experts don’t know yet whether the telescope survived the vibration without damage. Only the resonance search can tell. Previously the engineers have determined the frequencies at which parts of the instrument are oscillating in resonance. After the vibration, they repeat this procedure. Looking at the peaks of the two graphs when overlapping them reveals whether something has changed. A first quick look shows no sign of damage. Relieved most of the spectators leave the control room and let the engineers do their further analysis followed by the final random test at qualification level in z-axis.
The following day back in the clean room, the CHEOPS team removes the protective plastic sheets around the telescope and starts another alignment test to find out whether the vigorous shaking caused any small displacements that couldn’t be detected by the resonance search. «The telescope has maintained the initial alignment within the measurement accuracies. We were extremely happy to see this outcome and can state that the telescope is mechanically qualified for flight.» says Thomas Beck. «Everything went well,» summarizes Christopher Broeg: «This is a big step.»
Categories: Internal Newsletter, News